- Morning Machinist
- Posts
- "My Shop Doesn't Keep Carbide Endmills"
"My Shop Doesn't Keep Carbide Endmills"
by Morning Machinist
👷♂️ hireCNC Featured Companies / Jobs
Indianapolis, IN | Kodiak Mfg | CNC Machinist, CNC Programmer, CMM Programmer
Roscoe, IL | Schafer Industries | CNC Grinding Machinist, CNC Hob Machinist, CNC Milling Machinist, QC Tech, CNC Lathe Machinist
Rochester NY & Greenville OH | Arnold Magnetic Technologies | CNC Machinist, CNC Programmer, Prototype Machinist
🔧Community Weigh-In: Cutting Astralloy Without Carbide
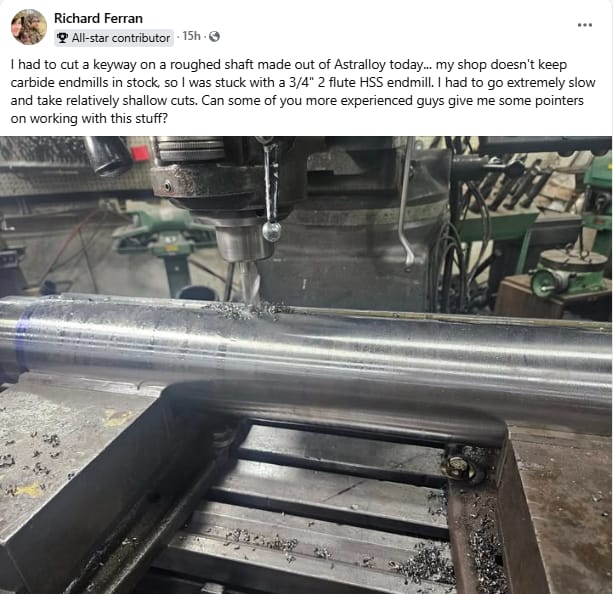
A machinist posted a rough day in the shop: tasked with cutting a keyway in Astralloy using only a 3/4" 2-flute HSS endmill, because the shop doesn’t stock carbide tooling. The response from the machinist community? Let’s just say... they didn’t hold back.
Here’s a breakdown of the top responses:
🛑 The Brutal Truth: Time to Rethink the Shop
Several machinists didn’t mince words — the overwhelming message was simple: “If your shop doesn’t stock carbide in 2025, it might be time to move on.” One even joked, “Holy Bedrock Machine Shop, Mr. Flintstone...”
Others put it more practically: carbide might cost more upfront, but the savings in time, tool life, and job quality make it the smarter investment. As one commenter put it:
“Fifty bucks in tooling saves five hundred in wages and gets me another job.”
🛠️ Tooling Hacks & Alternatives (If You’re Stuck)
Not everyone went straight to the résumé advice. Some offered real-world workarounds:
Use plunge cuts — "It’s called an END mill for a reason."
Start small when possible, like using a pilot drill for larger holes.
Add taller jaws for rigidity, slow down the feed/speed, and use solid coolant strategies.
If you’re equipped, grind single-point carbide tools from blanks using a cutter grinder — one shop did just that to stay productive with tough materials.
💡 Tooling Philosophy: Long-Term Thinking
One commenter highlighted the bigger picture:
“It costs to make.”
Tooling decisions don’t just affect one job — they shape shop reputation, quality, and long-term efficiency. If management won’t invest in proper tooling, it's not just your tools that are taking a beating — it’s your career trajectory.
Part Getting Jammed at Part-Off? Here’s How the Pros Prevent Crashes.
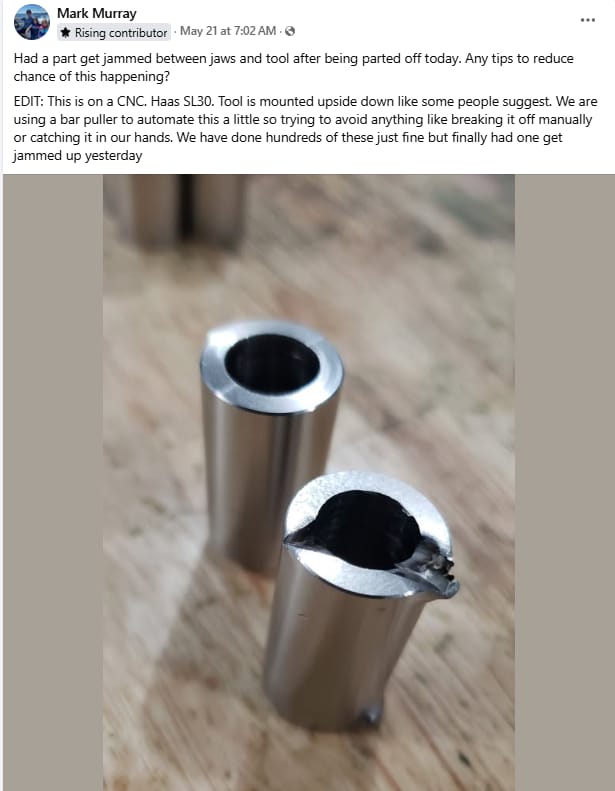
A machinist running a Haas SL30 shared their frustration after a part got wedged between the tool and the jaws during parting — something that hadn’t happened in hundreds of previous runs. The community chimed in with hard-earned tips, tool tweaks, and a few laughs.
🛠️ Modify the Parting Strategy
“Lower your rpm at the point where the part breaks off. Stop .05” before, lower the rpm then Continue. Drop it to 150rpm”
“Had this happen before on a job I ran 100’s of times. Shorten the distance between the jaws and the parting tool or leave a few thou shy of parting and tap off with hammer.”
🤲 Catch It
“I like to not part all the way off if I can’t catch it with something. Then just pop it off by hand after the spindle is off. Small parts I might make a spring out of banding straps that push the part down away from the pinch points.”
“Use wire in tailstock to catch it”
“I used a drill chuck with a rod chucked in it if the parts had holes, cut them off and slide them back and cut another etc,. On live centers I backed off the pressure of it when I was close to separation.”
🧰 Evaluate Your Puller & Tooling Setup
“What kind of bar puller are you using? Is it the 90 degree finger type or a releasing type like a Royal? If it the spring loaded finger type is the last part becoming lodged in the fingers? If so invest in a Royal or similar releasing puller, you can eliminate some severe crashes.”
“Yes we had the same problem, and being engineers, we didn't want to stand there all day with a stick catching them. We made thousands of a similar part and had two in a week get caught between the chuck jaw and the tool holder. Screwed the turret up badly. The parting tool was an adjustable blade type that protruded forward of the turret and the jaws had a flat face for full diameter. We turned the jaws so they had an "L" shape , giving a bit more clearance changed the toolholder so nothing was proud of the turret. Also slowed the speed to 500RPM for the last .5mm distance. Been fine since then. Sometimes shit happens.”
🧱 Remove the Gaps — Literally
“Don’t leave a gap for the part to fall into.
I read you are using a bar puller and idk how much you need to stick out from chuck for that but I’d leave the bare minimum.
Failing that remove the gap between the jaws, for example you could weld 6 triangles onto the existing jaws(1 each side of each jaw) to remove the gap the part fell into.
Or use a collet chuck to hold the part.”
😂 Machinist Wisdom (Or Something Like It)
“Smoke less pot.”
Machinists with questions or advice 🤔
⁉️ Does anyone have experience with beryllium copper?
⁉️How important is it to clean your machine?
⁉️ Any good machine shops in the Oklahoma City area?